In recent years, with the rapid rise of steam prices, the energy consumption in the evaporation process has sharply increased the cost burden of enterprises. At the same time, energy conservation, environmental protection, and emission reduction have become national events participated by the whole society. Therefore, it is very urgent to find an efficient and energy-saving evaporation concentration technology. Under this trend, mechanical steam recompression technology has developed rapidly. Mechanical steam recompression technology is a kind of heat pump technology, referred to as MVR or MVC. Today, let’s have a look at the application of Mechanical vapor recompression technology in different evaporation industries.
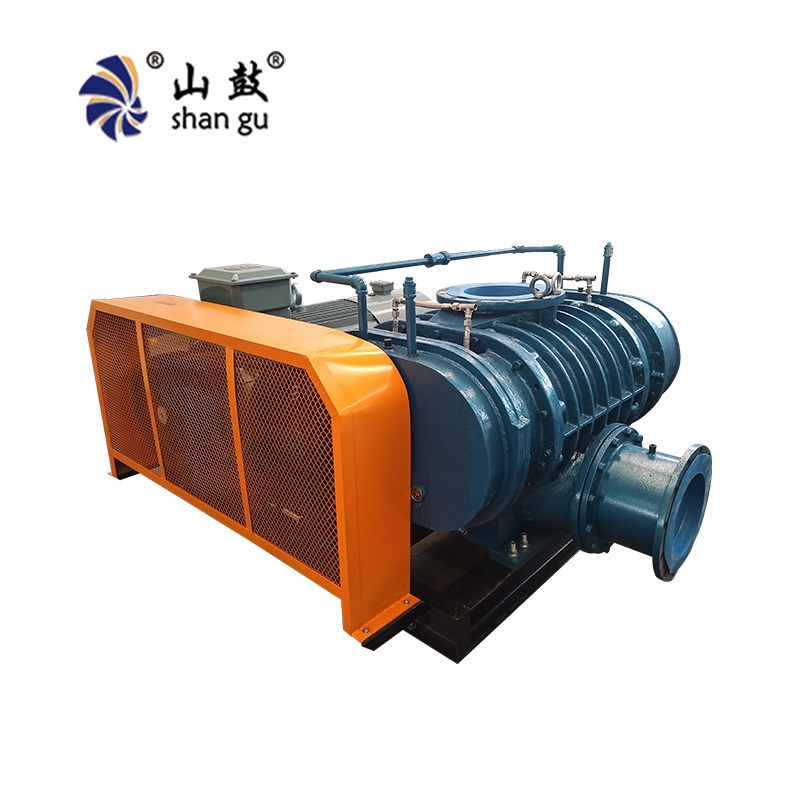
1. Introduction to MVR Technology
Figure 1 is A typical MVR evaporation process.
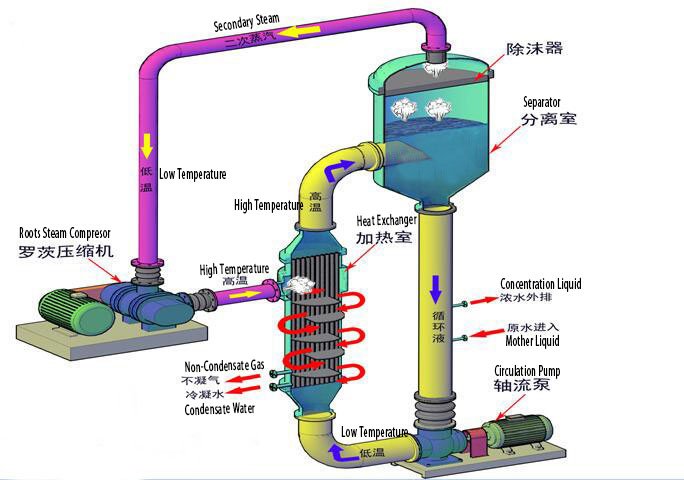
This technology is an economic energy integration technology, which reduces the waste of primary energy and the negative impact of a large number of cooling and heating requirements on the environment. It is also applicable to places without steam. Electric energy can be used to generate secondary steam. With a small amount of external work input into the system, a large amount of heat energy of low-pressure steam can be effectively utilized.
MVR evaporation technology has the following advantages:
(1) a small amount of fresh steam is consumed and the operation cost is low;
(2) less supporting public works and small floor space;
(3) easy start, simple operation, and stable operation;
(4) simple structure, low operation cost, and mild evaporation.
Domestic MVR technology has entered a period of rapid development. It has developed in many production fields, and some enterprises have made rapid progress in compressor technology, especially in centrifugal and roots steam compressors. They have gotten rid of the restriction of completely relying on imports, but it still needs a long-term development and performance improvement process.
2. Application progress of Mechanical Vapor Recompression-MVR technology in evaporation
2.1 Seawater desalination
The research of MVR technology abroad is relatively early, especially in the field of seawater desalination. China has done a lot of work in the introduction, digestion, technological innovation, and equipment manufacturing of seawater desalination, but compared with foreign countries, the scale of seawater desalination in China is not large, and there is still a big gap in research-level, innovation ability, and system design. At present, seawater desalination technology mainly includes reverse osmosis and distillation. Distillation mainly includes multistage flash distillation, low-temperature multi-effect distillation, and pressure steam distillation. Through the energy consumption estimation of three seawater desalination systems: multi-stage flash, low-temperature pressure steam distillation, and MVR heat pump cycle, the results show that the seawater desalination system uses the MVR heat pump cycle is the most energy-saving. The energy consumption per ton of water of a large-scale seawater desalination plant is about 8-12 kW / h.
2.2 Salt making
China’s salt-making technology is mainly multi-effect evaporation, and MVR salt-making technology is popular abroad, especially in Europe. Choosing MVR salt-making process can well solve the problem of a substantial increase in cost caused by the energy price rise in existing salt production. It is the best choice for salt-making enterprises to reduce energy consumption, improve product quality, reduce production cost and improve economic benefits. MVR salt making system mainly includes evaporation system, secondary steam washing system, steam compression system, compressed steam superheat elimination system, tank brine preheating system, centrifugal dehydration and drying system, condensate system, raw steam system, and other systems. The technical parameters mainly include heat balance, compression ratio, and effective temperature difference.
2.3 Wastewater Treatment
Many production fields will produce wastewater containing a large number of inorganic salts, such as sodium chloride, sodium sulfate, sodium carbonate, etc. These inorganic salts have always been one of the difficulties in wastewater treatment. If the inorganic salts in the wastewater are recycled, these inorganic salts can not only be used as raw materials in the production process, save costs, avoid waste of resources, but also avoid environmental pollution, Realize the recycling of resources. Aiming at the high concentration ammonium nitrate wastewater of the plant, process technologies such as physicochemical filtration, MVR evaporation concentration, and membrane purification are adopted to recycle it. The final concentrated liquid can be used for the production of chemical fertilizer. The freshwater can be used as the product water of the plant. This technology has good economic and environmental benefits.
Different types of wastewater treatment processes are different. The evaporation process of high concentration wastewater containing ammonium chloride produced in the production of basic copper chloride is studied. The multi-effect evaporation is changed into MVR evaporation. Compared with the three effect evaporation crystallizer, the enterprise can save 69% of standard coal and 69% of operation cost every year.
According to the principle of mechanical compression heat pump and rising film evaporation, a set of high-efficiency MVR heat pump evaporation alkali recovery systems is designed for the wastewater containing NaOH. The system not only recovers water and NaOH solution but also has a high energy utilization rate, high energy efficiency ratio, and more environmental protection compared with the traditional system. The cost can be recovered after one year of normal operation.
According to the characteristics of large oil field water consumption and high sewage temperature, a technical scheme of desalination treatment of oil field sewage with MVR technology is proposed. It is found that the compression ratio of the compressor is the main factor affecting power consumption. With the increase of the heat transfer temperature difference, the total specific heat transfer area decreases linearly and the specific power consumption of the compressor increases linearly. Therefore, the heat transfer temperature difference needs to be optimized. This method has the characteristics of compact equipment, no external heat source and cooling water, and a relatively flexible scale. The copper etching wastewater containing ammonia nitrogen, COD, chloride ion, and other pollutants are studied. After pretreatment, the wastewater enters the MVR evaporation system to produce ammonium chloride products. The distilled water can meet the effluent standard after being treated by ion exchange resin.
The double effect MVR evaporator is used to study the treatment of high concentration ammonium sulfate wastewater. A mathematical model is established based on mass balance and energy balance. It is found that it is reasonable to control the temperature rise at 2.5-4 ℃. The power consumption reaches the minimum under the condition of 32% mass fraction of primary effect discharge liquid.
2.4 Total halogenated caustic soda
The production of chlor alkali has the characteristics of high energy consumption and pollution. Therefore, the caustic soda industry must adopt the ion-exchange membrane caustic soda process. In order to use this process to realize total halogen caustic soda, it is necessary to treat light brine to close to saturation. Water removal methods include membrane filtration, multi-effect evaporation, MVR evaporation, and light brine return to the well. A company in Chongqing has selected the MVR evaporation process, which has obvious economic benefits. It has expanded the scale of primary brine, reduced the amount of primary brine refining agents and the number of secondary brine regeneration. The quality of steam condensate produced is high and can be used as desalted water. The steam condensate and concentrated brine produced by the system can exchange heat with brine, and the corrosion to the equipment is less than that of multi-effect evaporation, Make full use of all the heat. It should be noted that the free chlorine in the light brine should be removed, and the impurities should be regularly discharged to the brine storage tank for treatment.
A Chlor Alkali Company in Lianyungang has realized the total brine alkali making process by using ceramic brine filtration technology, introducing SR’s membrane denitration, and MVR light brine concentration technology. Among them, MVR evaporation plays an important role. A large amount of distilled water produced in the process reduces the production water required for salt melting. At the same time, this part of distilled water is used in the electrolytic cell, which reduces the consumption of pure water in the caustic soda plant and tap water. It realizes the saving of water resources, and reduces the steam consumption required for salt melting.
2.5 Other evaporation Application of Mechanical Vapor Recompression
MVR evaporation technology also has many applications in other fields, such as the concentration of fruit and vegetable juice, the evaporation of orange juice, the evaporation of amino acid fermentation broth, etc. Compared with the traditional three-way evaporator, the traditional three-way steam consumes 9 million yuan of steam, 500000 yuan of circulating water and 1.5 million yuan of power consumption of MVR evaporator. Therefore, the annual use of MVR technology can save 8 million yuan, with obvious energy saving.
3. Research progress of Application Mechanical Vapor Recompression
As the core of the MVR evaporation system, domestic compressors are mainly imported, including Sulzer, TUTHILL, Siemens, Piller, Dresser roots, and other well-known foreign fan and compressor brands. In recent years, China has conducted relevant research on the industrial transformation and production application of MVR compressors. They have accumulated a lot of valuable experience for the localization of MVR compressors. The localization of steam compressor has the ability of relevant equipment design, machining, and process design. The current development trend of MVR compressor is mainly centrifugal compressor and roots compressor. Centrifugal compressor is applicable to the working condition of large flow and small temperature rise. At present, it is most used, but attention should be paid to prevent surges. Roots compressor is suitable for handling the working condition of small flow and large temperature rise. It is not sensitive to dust. But if the seal is not good, it is easy to produce oil and gas pollution.
Using MVR evaporation, the reasonable temperature rise range is 8-20 ℃. If the boiling point rises above 18 ℃, the advantage of MVR evaporation is no longer obvious. For the working condition with insufficient temperature rise, the compressor in series can be selected under the condition of reasonable input. But the matching problem of inlet and outlet pressure of centrifugal compressor in series needs to be solved. For the working condition with the insufficient flow, the parallel compressor or multi-stage axial compressor can be selected.
In the future, the research on the compressor in MVR evaporation should be improved from the aspects of large processing capacity and corrosion resistance. The research direction of the roots compressor is the coating required by the roller, and strive to develop materials with higher cost performance than the existing nickel, chromium coating, and polymer coating, so as to improve the overall quality of the compressor. For the centrifugal compressor, the structural design of impeller directly determines the performance of compressor. The optimal design of impeller needs to be further studied.
4. Conclusion-Application Mechanical Vapor Recompression
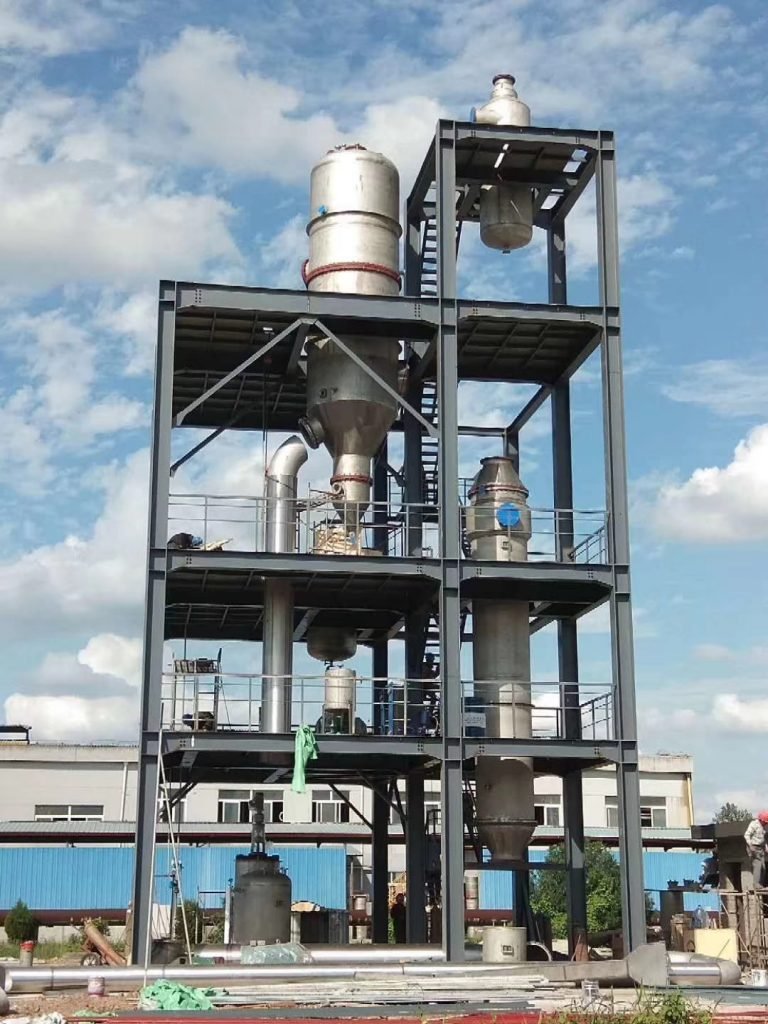
MVR technology is characterized by consuming a small amount of mechanical work to reuse the steam generated in the evaporation process. The key point is that the vaporization latent heat of steam is a weak function of its saturation pressure. For single effect MVR evaporation, its pressure loss is actually very small. Therefore, we can recompress the “exhaust steam”.
Through the comparison of the three-way evaporator, traditional heat pump three-way evaporator (CHP), and MVR heat pump three-way evaporator (AHP), the results show that the second and third forms can reduce energy consumption and waste heat emission. Compared with the first working condition, the heat pump system with MVR has excellent performance. The heat demand and heat loss are reduced by 15.7% and 22.7% respectively 6%, effectively reducing the environmental heat load. Similarly, the waste heat of high-temperature sewage is recovered. Before the high-temperature sewage is sent to the wastewater treatment plant, it is treated by vacuum evaporation and MVR technology. After optimization, the energy efficiency ratio can reach 41.4. The CO2 emission can be reduced by 143 670 kg per year.
MVR evaporator is a mature technology. At present, the key to its rapid development is how to find a suitable application, but its potential is huge. In the future, it will be mainly used in environmental protection, chemical industry, food, and other industries. These industries require large flow and low compression ratios, especially for enterprises that need to expand or transform evaporation equipment due to insufficient steam and water supply capacity and insufficient site, as well as low-temperature evaporation occasions. However, the main purpose of MVR evaporator is to reduce the operation cost and make it lower than other forms. Therefore, before use, the balanced relationship between investment cost and operation cost should be calculated for each specific working condition. Generally, the investment cost should be recovered within 1.5-2 years.
According to the development trend of energy prices, the gap between steam and electricity costs will become larger and larger. With the national demand and support for the environmental protection market, more and more compressor manufacturers will invest in it. The localization pace of MVR will be accelerated, the advantages will be more and more obvious. The application space will be wider, The application of mechanical steam recompression technology is the key research content in the field of evaporation in the future.
This article mainly introduces the application progress of the mechanical vapor recompression ( MVR) evaporation technology both in China. They include ly in the field of seawater desalination, production of salt, treatment of wastewater ( ammonium nitrate, ammonia chloride, ammonium sulfate, oilfield sewage, etc. ), alkali with whole marinating and other fields of application.